Cet article décrit l’utilisation de CIVA SHM pour réaliser des simulations d’implantations d’un réseau de capteurs par ondes guidées afin de détecter des défauts sur un panneau composite. Une réalisation Extende !
1) Contexte, problématique à résoudre :
Le Structural health monitoring (SHM) par ondes guidées permet le suivi santé des structures au cours du temps. Dans un contexte où les capteurs sont embarqués dans la structure à contrôler, avec un nombre important de paramètres influents (capteurs utilisés, leur implémentation, défauts à détecter, variations d’environnement, etc.) et une mise en œuvre complexe et coûteuse, les campagnes expérimentales deviennent rapidement prohibitives pour conduire de réelles études d’optimisation et de fiabilité.
Le recours à la simulation apparait alors comme un outil incontournable pour réaliser des essais intensifs et ainsi aider à concevoir les dispositifs SHM, démontrer leurs performances, définir et ajuster les seuils de détection afin d’optimiser la probabilité de détection des défauts tout en limitant le taux de fausses alarmes.
Une des voies de déploiement des solutions SHM en applications industrielles concerne le suivi des panneaux composite déployés dans les structures aéronautiques, thématique illustrée ci-après dans ce cas d’application.
2) L’outil de modélisation CIVA pour le SHM :
CIVA est une plate-forme logicielle multi-technique largement utilisée dans le monde pour la simulation numérique des méthodes d’Essais non destructifs (ultrasons, ondes guidées, radiographie, tomographie, courant de Foucault, thermographie).
Le SHM par ondes guidées a intégré récemment cette plate-forme « métier ». Le module de simulation SHM permet d’adresser le monitoring de structures tubulaires métalliques et de panneaux métalliques ou composites, présentant potentiellement des courbures, ou des éléments de type raidisseur.
CIVA est développé par le CEA et distribué mondialement par la société EXTENDE [1]. CIVA SHM utilise une combinaison optimisée d’Éléments Finis Spectraux et de macro-maillage [2] qui démontre des performances très compétitives, avec un gain constaté d’un facteur supérieur à 100 par rapport aux temps de calculs obtenus avec des outils de simulation par éléments finis généralistes [3], ainsi que des gains du même ordre de grandeur en termes de mémoire vive.
Comme pour tout logiciel de simulation, il est important de pouvoir s’appuyer sur des éléments de validation expérimentale afin de vérifier la pertinence des modèles utilisés dans un contexte donné et utiliser la simulation avec confiance pour un projet industriel. Différentes études de validation ont été menées récemment autour de CIVA SHM [3], [4]. Le cas de validation de CIVA SHM présenté dans cet article s’appuie sur les données expérimentales fournies par l’initiative « Open Guided Waves » [5].
Le macro-maillage permet un gain d’un facteur supérieur à 100 par rapport aux temps de calculs par éléments finis généralistes, et des gains du même ordre de grandeur en termes de mémoire vive !
2.1 Pièce utilisée pour ce cas test
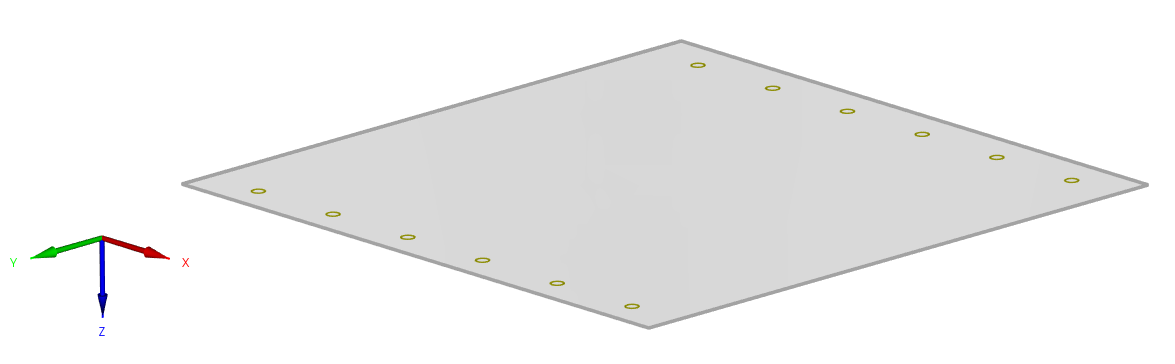
La pièce inspectée dans cette application est une plaque composite de type carbone-époxy de dimension 500 mm x 500 mm et d’épaisseur 2 mm répartie sur 16 couches.
Ce type de structure revêt des propriétés élastiques anisotropes vis-à-vis de la propagation des ondes ultrasonores guidées, ce qui est pris en compte dans la modélisation. 12 patchs piézo-électriques de diamètre 10 mm sont installés sur la structure, comme illustré sur la figure 1 ci-contre.
2.2 Paramètres testés
Différentes fréquences d’excitation ont été utilisées, les sondes étant successivement excitées en émission pendant que les 11 autres sont en réception. Les figures ci-dessous comparent les résultats mesurés et simulés des signaux reçus par l’ensemble des récepteurs pour une excitation à 40 kHz des traducteurs #1, #3 et #8 (matérialisés par un point rouge sur la représentation schématique de la pièce). Les résultats sont présentés sous forme d’imagerie B-Scan (chaque colonne représente le signal reçu par un capteur donné, le B-Scan simulé étant affiché sous le B-Scan expérimental) puis chaque signal temporel reçu est illustré (simulation en rouge, expérience en bleu).
A noter : Les données expérimentales et simulées illustrées ci-dessous sont normalisées par rapport au maximum d’amplitude mesuré/simulé sur l’ensemble des voies en réception sans la voie pulse-écho.
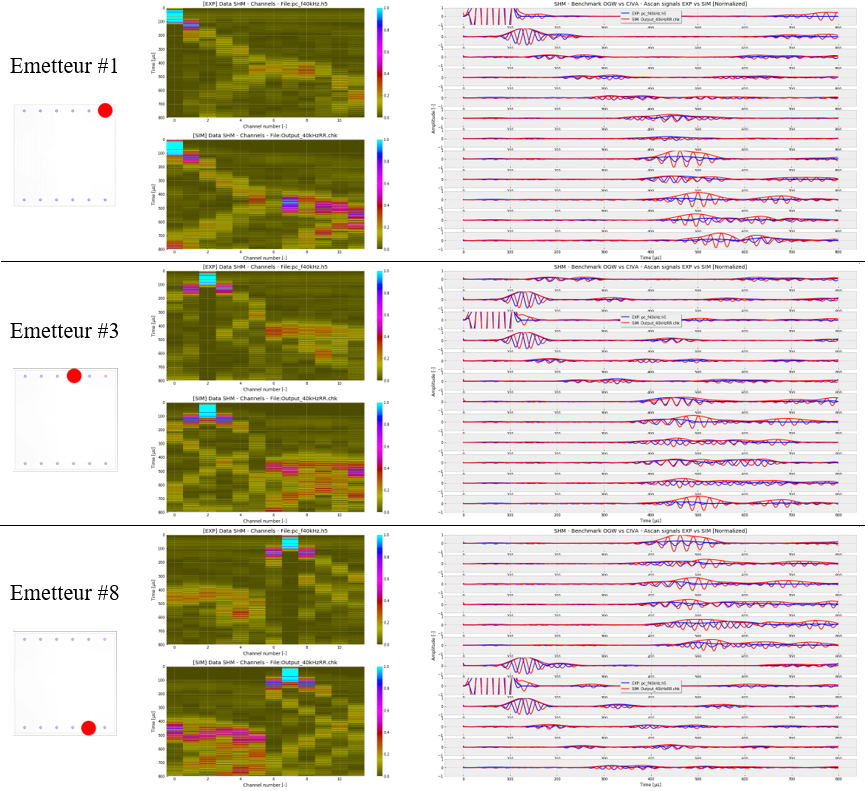
La comparaison montre un bon accord des signaux calculés avec les mesures : les différents modes propagés sont bien représentés (mode de type S0 plus rapide d’abord, puis mode A0), les temps de vol, la forme du signal ainsi que ses différentes composantes dues aux interactions avec les bords de pièces apparaissent tout à fait représentatives des mesures.
Les courbes de dispersion calculées par CIVA SHM sont présentées ci-dessous pour ce cas d’application. Les caractéristiques du mode A0 apparaissent en rouge (vitesse de 1280 m/s et longueur d’onde de 19 mm à 40 kHz) et le mode S0 en bleu (vitesse de 3400 m/s et longueur d’onde de 85 mm à 40 kHz). Le matériau composite étant anisotrope, une représentation polaire des vitesses de groupe en fonction de l’angle du parcours sonore dans le plan de la pièce est fournie.
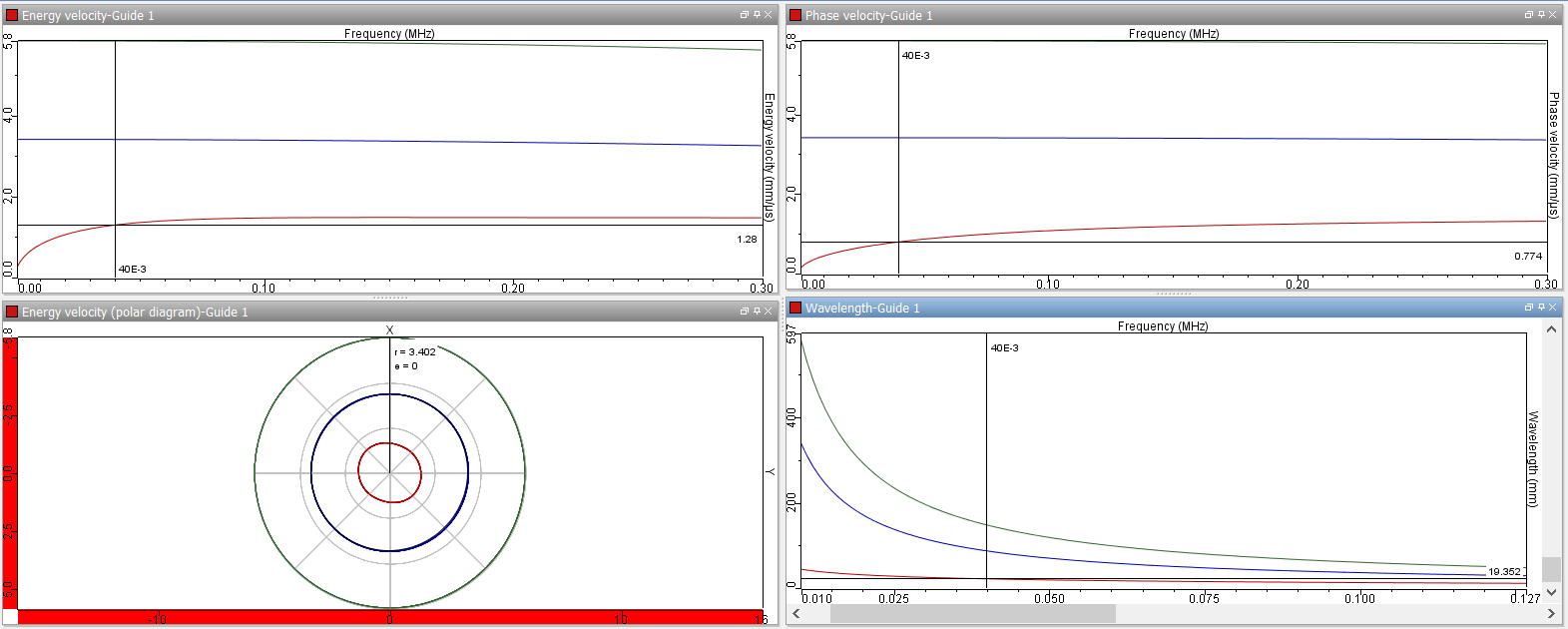
La modélisation n’est toutefois jamais le reflet exact d’une mesure compte-tenu d’une part des approximations inhérentes au modèle mais aussi d’autre part des incertitudes liées à la mesure. On peut citer ici notamment :
– les incertitudes liées à la prise en compte des conditions de rebonds sur les bords de pièce (supposées parfaites en simulation) d’autant plus que les capteurs sur cet exemple sont situés à proximité de ces bords,
– et le fait que la modélisation actuellement réalisée néglige l’atténuation de l’onde, sensible lorsque les distances de propagation sont grandes et les fréquences plus élevées.
L’accord entre simulation et expérience apparait cependant tout à fait satisfaisant pour valider l’emploi de CIVA SHM sur ce cas d’application et prédire les modes transmis et les interactions avec la pièce et d’éventuels défauts.
Plus de détails sur ces validations sont données dans [4].
3) Résultats obtenus :
La détection des défauts en SHM par ondes ultrasonores guidées repose sur le traitement des signaux émis et reçus par l’ensemble du réseau de capteurs afin de déceler une modification par rapport un état de référence supposé sans défaut. Cette analyse peut se faire directement sur les signaux temporels par soustraction de signal de référence et traitement de signal. Cependant, des outils d’imagerie existent également afin de donner une information plus riche et compréhensible pour la détection et la localisation d’une anomalie. La technique d’imagerie utilisée peut révéler de potentiels artefacts dus à la fois à la méthode d’imagerie elle-même ou à des signaux parasites (par exemple liés aux rebonds en bord de pièce).
3.1 Influence de la distance capteur – bord de pièce
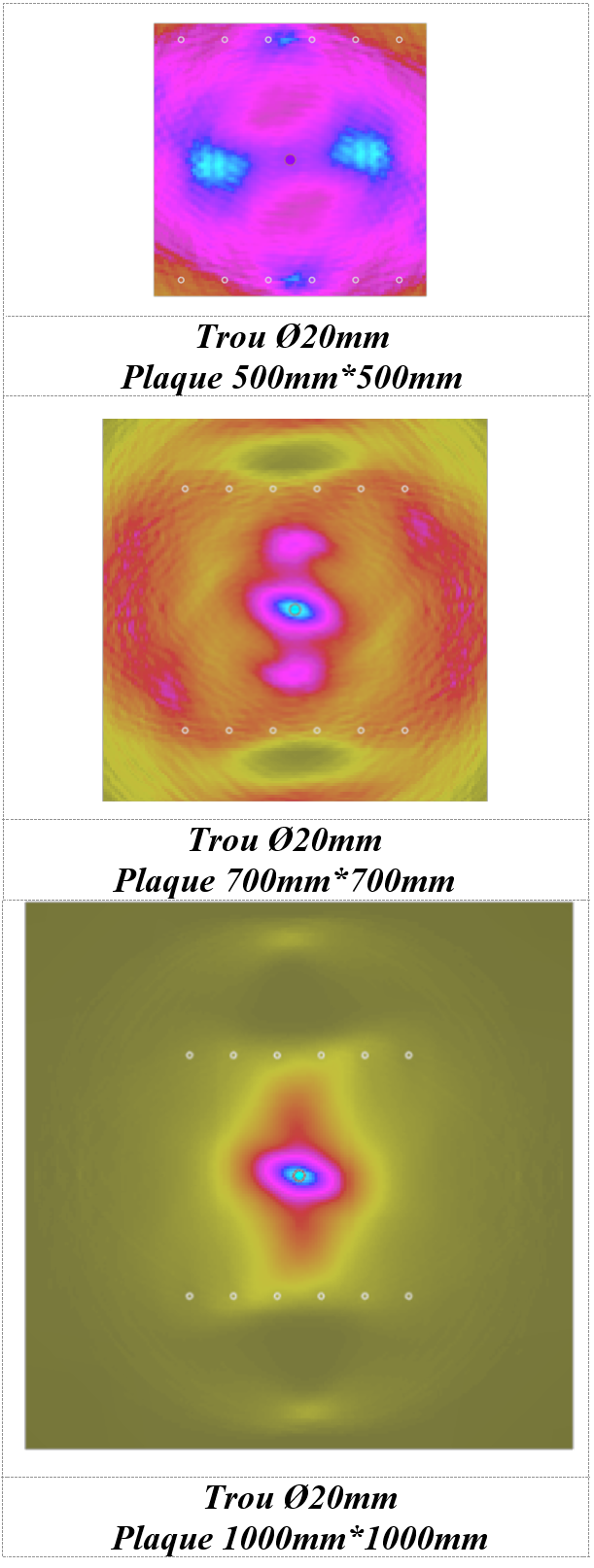
Il est possible de comparer les images reconstruites obtenues dans CIVA SHM en simulant un trou traversant :
– de diamètre 20 mm
– positionné au milieu de la plaque composite
– pour le réseau de capteurs présentés précédemment (diamètre 10 mm)
– pour 3 dimensions de plaques différentes : 500 x 500 mm (cf. cas de validation), 700 x 700 mm et 1000 x 1000 mm.
La reconstruction est basée sur l’exploitation du mode A0. L’impact de la taille de la plaque et donc de la distance entre le réseau de capteurs et les bords de pièce apparait clairement, la tâche constituée par le défaut est bien mieux identifiée et résolue pour les 2 dimensions supérieures que pour la taille initiale où la détection du défaut sur la base de l’image parait très délicate. Lorsque c’est possible (et selon la position du défaut recherché dans la pièce), il paraît donc pertinent d’éviter une trop grande proximité entre l’instrumentation et les bords de pièce ou d’utiliser des algorithmes d’imagerie capables de traiter de façon pertinente les réflexions des paquets d’ondes sur les bords.
La mise au point de l’instrumentation inclut notamment le choix du nombre de capteurs et leur disposition sur la pièce : un trop faible nombre de sondes réduit la probabilité de détection et la capacité de caractérisation, tandis qu’un trop grand nombre de sondes conduit à un coût d’installation rédhibitoire pour son déploiement industriel.
La simulation permet d’étudier en amont la performance obtenue en fonction de différentes stratégies d’implantation des capteurs, rapidement et à faible coût, car sans avoir à instrumenter de pièces réelles, permettant ensuite de tester expérimentalement uniquement les solutions prometteuses.
3.2 Influence du nombre de capteurs
La comparaison peut être faite avec des images reconstruites obtenues pour 12, 8, 6 ou 4 capteurs (diamètre 20 mm) en disposition circulaire à une certaine distance du trou de la plaque composite. La qualité de l’image du défaut obtenue (ou capacité d’identifier un signal de défaut et de l’isoler des signaux parasites), donc la probabilité de détection et la capacité de localisation voire de dimensionnement de celui-ci, reste satisfaisante jusqu’à 6 capteurs mais se dégrade sensiblement pour 4 capteurs avec la disposition de sondes choisie ici.
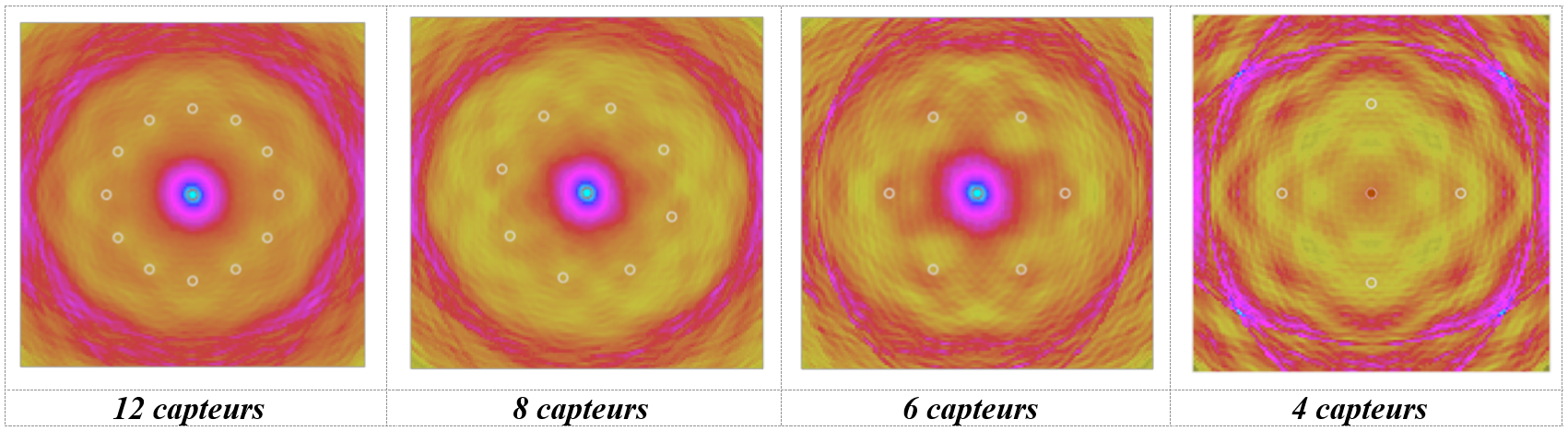
3.3 Influence de la disposition du réseau de capteurs
Les images reconstruites ci-dessous sont obtenues pour le trou dans la pièce composite avec différentes dispositions d’un réseau de 12 sondes (diamètre 20 mm) : soit alignées, soit en schéma circulaire, soit en introduisant une disposition en quinconce plus ou moins marquée.
La figure 6 ci-après montre que la qualité de la reconstruction du signal du défaut s’améliore sur ce cas (moins d’artefacts et donc de zone « morte ») lorsqu’on tend à briser une trop grande symétrie sur la disposition des traducteurs ou lorsque le défaut n’est pas centré par rapport au réseau de capteurs.
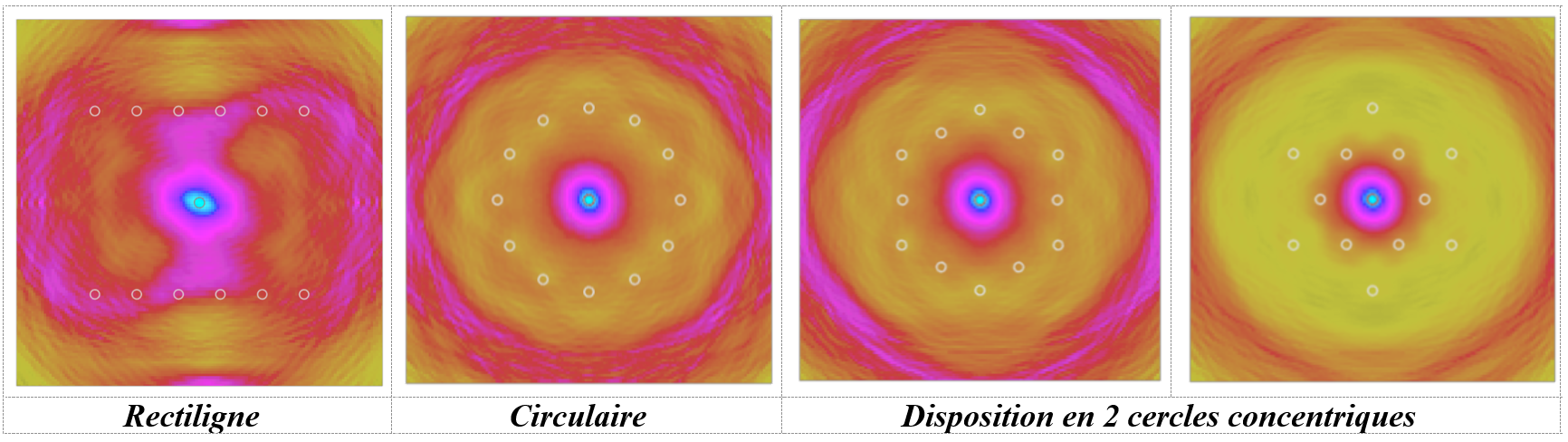
La mise au point du schéma d’instrumentation inclut bien évidemment également le choix des capteurs (technologie, taille, type d’excitation). Il convient notamment de générer des modes ayant une longueur d’onde adaptée par rapport au défaut à détecter et caractériser.
3.4 Résultats avec un défaut de type délaminage
La simulation s’est aussi intéressée à la recherche d’un délaminage plus représentatif des types de défauts à détecter dans ce type de structure composite. De tels délaminages peuvent notamment survenir à la suite de chocs rencontrés par la structure en fonctionnement. Dans un premier temps, un délaminage de forme elliptique de dimensions 96 mm x 48 mm et propagé sur 6 inter-plis successifs a été modélisé, cf. figure 7 ci-dessous.

Ci-dessous (figure 8) peuvent être observées les signatures de ce défaut, obtenues pour différentes fréquences d’excitation (40 et 100 kHz, longueurs d’onde respectives du mode A0 de 19 mm et 10 mm) et différents diamètres de sondes (18 mm, 10 mm, 5 mm).
A la fréquence 40 kHz, l’image reconstruite en exploitant le mode A0 fait apparaître un signal net à l’emplacement du défaut, néanmoins assez mal résolu par rapport à la forme et la dimension du défaut lui-même, quel que soit le diamètre des sondes simulées.
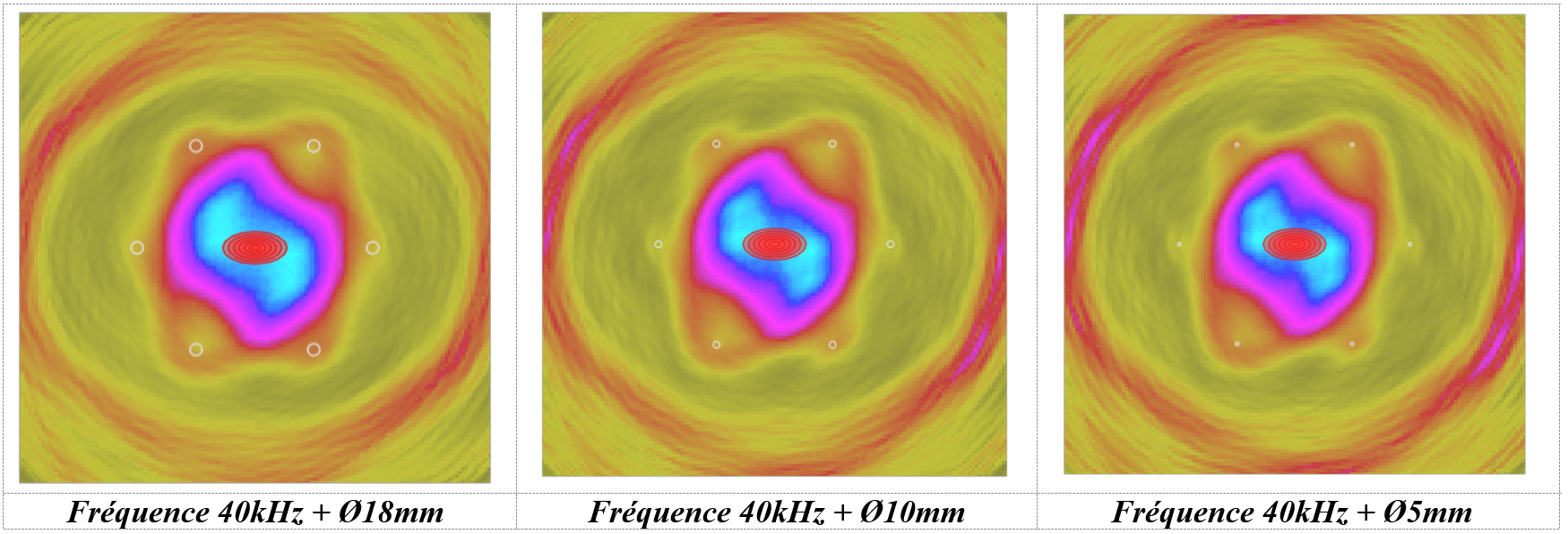
En revanche, pour une fréquence plus élevée (100 kHz), une indication plus proche des dimensions réelles du délaminage existant est obtenue. De plus, l’image du défaut avec les capteurs de plus petites dimensions (diamètre 10 et 5 mm) est davantage optimisée.
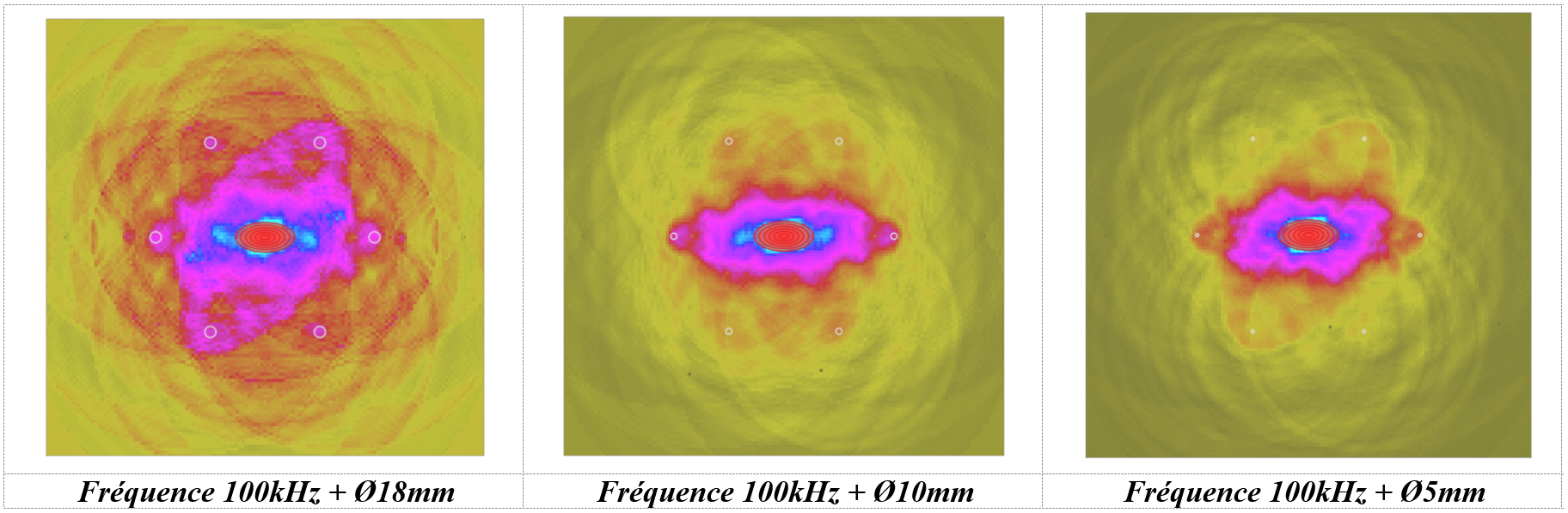
Un bon compromis serait donc une instrumentation basée sur 6 sondes de fréquence 100 kHz et de diamètre 10 mm afin d’optimiser la détection et la caractérisation de ce délaminage étudié.
Naturellement, les performances de détection et de caractérisation d’un tel dispositif d’instrumentation dépendent fortement de la nature et de la dimension de l’indication de défaut recherchée. La figure 10 ci-dessous illustre les reconstructions obtenues par ce même dispositif d’inspection (6 sondes en cercle, fréquence 100 kHz, diamètre 10 mm) lors de l’inspection de différentes dimensions de délaminage elliptique sur 6 plis consécutifs : 96 x 48 mm, 48 x 24 mm, et 24 x 12 mm.
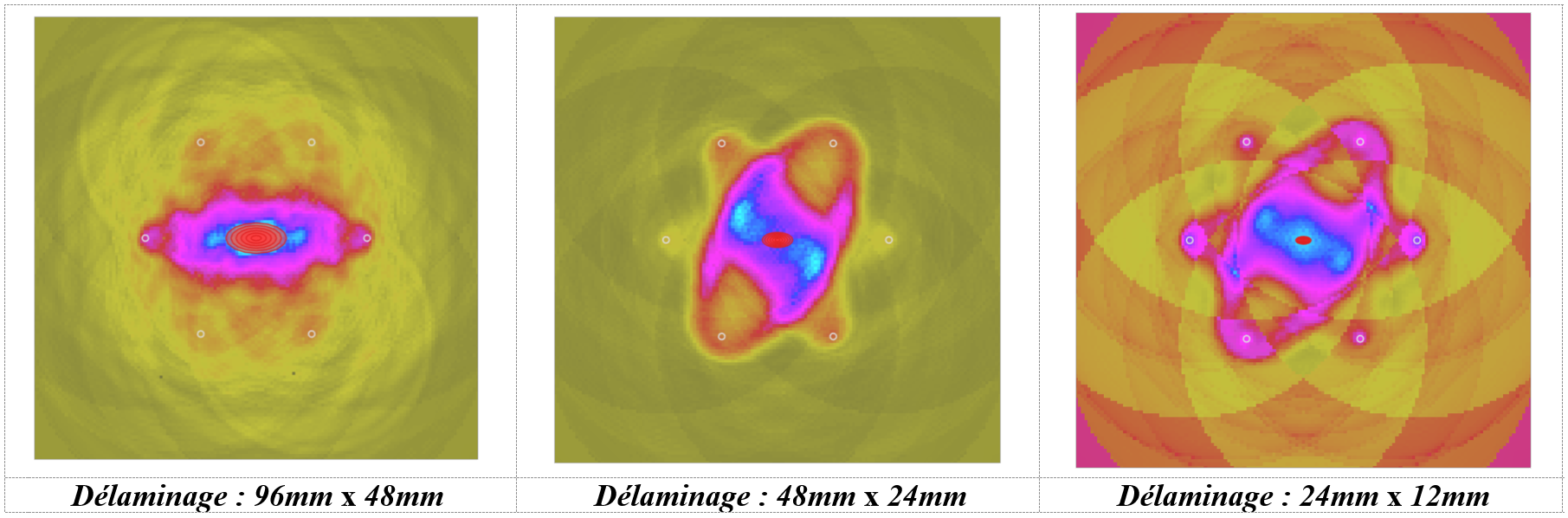
Ces simulations montrent que ce dispositif d’inspection reste pertinent pour la détection de plus petits délaminages (une indication de défaut est visible). En revanche les capacités de caractérisation de l’indication par ce dispositif sont très nettement dégradées plus le délaminage simulé est petit. La simulation permet dans ce sens une meilleure compréhension, caractérisation et justification des performances et limites d’un dispositif de contrôle SHM donné selon le défaut recherché, à partir duquel il est possible de travailler sur des optimisations.
De plus, ces images ont été obtenues en supposant le réseau de sondes centré autour du défaut. Si une bonne connaissance des matériaux et des contraintes subies par la structure permet d’anticiper des zones préférentielles pour le développement des défauts, il est néanmoins délicat de prévoir exactement où ceux-ci vont véritablement s’initier. Une fois le modèle de simulation mis en place, il est aisé de prédire l’influence de la position du défaut inspecté sur sa détection et caractérisation pour un réseau de sondes fixées et donc d’évaluer davantage la robustesse du schéma d’instrumentation. Il serait beaucoup plus délicat et coûteux de construire autant de maquettes instrumentées que de positions de défauts supposées pour étudier cet aspect par une méthode purement expérimentale.
4) Conclusion
Après une présentation d’éléments de validation de CIVA SHM, différents exemples de simulations ont été présentés pour illustrer la détection de défauts en SHM par ondes guidées sur une plaque composite selon différents paramètres : distance des capteurs aux bords de pièce, impact du nombre et de la localisation des capteurs, « signature de différents défauts », taille et fréquence des capteurs.
Il en ressort que la modélisation constitue un outil puissant pour aider au développement et à la qualification des dispositifs de monitoring.
La modélisation ne prétend pas se substituer aux phases d’essais expérimentaux et de prototypage mais elle permet d’élargir considérablement le nombre de cas explorés. Plus qu’une compétition, c’est une complémentarité entre simulation et expérience qu’il faut mettre en avant : expérimentalement, il serait couteux de concevoir beaucoup de maquettes, qui plus est avec différents types de dommages et avec une instrumentation implémentée sur chacune d’entre elles.
En revanche, des mesures sur maquette permettent de rendre compte d’un monitoring réel de façon représentative et de suivre l’impact de variations des paramètres environnementaux sur la mesure (température, contraintes, vieillissement des structures, etc.). S’il est plus délicat de rendre compte de l’impact de ces paramètres environnementaux en simulation sans des modèles adaptés, il est par contre aisé d’introduire différents types de défauts dans un modèle, de faire varier ses caractéristiques (position, taille, forme), de tester différents designs de capteurs et de schéma de monitoring et de constituer des jeux de données de taille suffisante lorsqu’il s’agit d’établir des performances de détection de façon statistique et de travailler sur la qualification d’un procédé.
CIVA SHM offre ainsi aux acteurs du SHM un outil métier, présentant des temps de simulation performants et compatibles avec une utilisation intensive dans un contexte industriel.
Références
[1] www.extende.com ; www.extende.com/structural-health-monitoring-with-civa
[2] Imperiale, Alexandre, and Edouard Demaldent. « A macro‐element strategy based upon spectral finite elements and mortar elements for transient wave propagation modeling. Application to ultrasonic testing of laminate composite materials. » International Journal for Numerical Methods in Engineering 119.10 (2019): 964-990.
[3] Mesnil, O., Imperiale, A., Demaldent, E., & Chapuis, B. (2019, May). Validation of spectral finite element simulation tools dedicated to guided wave based structure health monitoring. In AIP Conference Proceedings (Vol. 2102, No. 1, p. 050018). AIP Publishing LLC.
[4] Mesnil, O., Recoquillay, A., Druet, T., Serey, V. Hoang, H. Imperiale, A. & Demaldent, E. (2021). Experimental validation of transient spectral finite element simulation tools dedicated to guided wave based structural health monitoring. Journal of Nondestructive Evaluation, Diagnostics and Prognostics of Engineering Systems, American Society of Mechanical Engineers, In press, 10.1115/1.4050708. hal- 03187419
[5] Moll, Jochen, et al. « Open guided waves: online platform for ultrasonic guided wave measurements. » Structural Health Monitoring 18.5-6 (2019): 1903-1914. http://openguidedwaves.de
Cet article a été rédigé par Fabrice FOUCHER et Bastien CLAUSSE (EXTENDE)